De acordo com a MIT News, aproximadamente um quarto das emissões de gases de efeito estufa veio da indústria da manufatura em 2020. Logo, as fábricas também podem esgotar as reservas locais de água e gerar grandes quantidades de resíduos, alguns dos quais podem ser tóxicos. Para abordar estas questões e impulsionar a transição para uma economia de baixo carbono, novos produtos e processos industriais devem ser desenvolvidos juntamente com tecnologias de manufatura sustentáveis. John Hart, professor de engenharia mecânica e diretor do Laboratório de Manufatura e Produtividade do MIT, vê os engenheiros mecânicos desempenhando um papel crucial nessa transição.
“Os engenheiros mecânicos podem resolver problemas críticos de forma exclusiva que exigem tecnologias de hardware de última geração e saber como dimensionar suas soluções”, diz Hart.
Várias empresas de rápido crescimento fundadas por professores e ex-alunos do Departamento de Engenharia Mecânica do MIT oferecem soluções para o problema ambiental da manufatura, abrindo caminho para um futuro mais sustentável.
Confira algumas das soluções criadas por startups fundadas a partir do MIT:
Gradiant: soluções de água Cleantech
Uma fábrica de produção de semicondutores de tamanho médio usa mais de 10 milhões de galões de água por dia. Num mundo cada vez mais assolado por secas, esta dependência da água representa um grande desafio. Considerando isso, a Gradiant desenvolveu uma solução.
“Quando a qualidade da água varia no sistema, nossa tecnologia envia automaticamente um sinal para os motores dentro da usina para ajustar as taxas de fluxo para trazer de volta o número adimensional para um valor de um. Uma vez que é trazido de volta ao valor de um, você está funcionando em condições ideais”, explica Govindan, que atua como diretor de operações da Gradiant. Este sistema pode tratar e limpar as águas residuais produzidas por uma fábrica para reutilização, economizando milhões de litros de água a cada ano.
Continua depois da publicidade |
Agora a empresa oferece várias soluções de tratamento de água e efluentes para clientes em setores como farmacêutico, energia, mineração, alimentos e bebidas e a crescente indústria de semicondutores. Com 450 estações de tratamento de água e esgoto construídas até hoje, a Gradient trata o equivalente a 5 milhões de residências de água por dia.
De acordo com a publicação, a taxa média de reciclagem na produção de semicondutores - ou fábricas - em Cingapura é de apenas 43%. Usando as tecnologias da Gradiant, essas fábricas podem reciclar de 98% a 99% dos 10 milhões de galões de água de que precisam diariamente. Essa água reutilizada é pura o suficiente para ser colocada de volta no processo de manufatura.
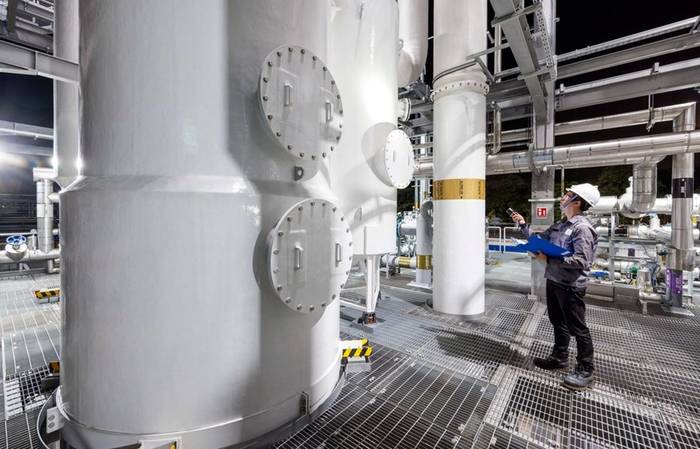
Via Separations: filtragem química eficiente
A filtração industrial é feita pelo aquecimento de produtos químicos em temperaturas muito altas para separar os compostos. A pesquisadora PHD Shreya Dave, que concentrou-se na dessalinização para sua tese de doutorado, compara isso a fazer macarrão fervendo toda a água até que ela evapore e tudo o que reste é o macarrão. Na manfatura, esse método de separação química é extremamente intensivo em energia e ineficiente.
A Via Separations criou o equivalente químico de um “coador de macarrão”. Em vez de usar calor para separar, suas membranas coam compostos químicos. Este método de filtragem química usa 90% menos energia do que os métodos padrão.
Enquanto a maioria das membranas é feita de polímeros, as membranas da Via Separations são feitas com óxido de grafeno, que pode suportar altas temperaturas e condições adversas. A membrana é calibrada de acordo com as necessidades do cliente, alterando o tamanho dos poros e ajustando a química da superfície.
“Esse sistema de circuito fechado é responsável por uma enorme quantidade de consumo de energia nos EUA. Podemos tornar esse processo 84% mais eficiente colocando o 'coador de macarrão' na frente da caldeira”, afirma Shreya Dave.
VulcanForms: manufatura aditiva em escala industrial
“Desenvolvemos uma arquitetura de máquina para manufatura aditiva de metal que pode construir peças com qualidade e produtividade excepcionais”, diz Hart. “E integramos nossas máquinas em um sistema de produção totalmente digital, combinando AM, pós-processamento e usinagem de precisão”.
Ao contrário de outras empresas que vendem impressoras 3D para outros produzirem peças, a VulcanForms fabrica e vende peças para seus clientes usando sua frota de máquinas industriais. A qualidade e precisão com que a VulcanForms produz peças é crítica para produtos como implantes médicos, trocadores de calor e motores de aeronaves. Suas máquinas podem imprimir camadas de metal mais finas que um fio de cabelo humano.
As tecnologias desenvolvidas na VulcanForms podem ajudar a levar a uma maneira mais sustentável de fabricar peças e produtos, tanto diretamente por meio do processo aditivo quanto indiretamente por meio de cadeias de suprimentos mais eficientes e ágeis.
Uma maneira pela qual VulcanForms e AM em geral promovem a sustentabilidade é por meio da economia de material.
Muitos dos materiais que o VulcanForms usa, como ligas de titânio, requerem muita energia para serem produzidos. Quando as peças de titânio são impressas em 3D, substancialmente menos material é usado do que em um processo de usinagem tradicional. Essa eficiência de material é onde Hart vê o AM causando um grande impacto em termos de economia de energia.
“As empresas que buscam diminuir o risco e dimensionar as tecnologias de energia limpa exigem know-how e acesso à capacidade da maufatura avançada, e a manufatura aditiva industrial é transformadora nesse aspecto”, acrescenta Hart.
LiquiGlide: reduzindo o desperdício, removendo o atrito
A LiquiGlide projeta revestimentos personalizados que permitem que os líquidos “deslizem” nas superfícies. Até a última gota de um produto pode ser usada, seja espremida de um tubo de pasta de dente ou drenada de um tanque de 500 litros em uma fábrica. Tornar os recipientes sem fricção minimiza substancialmente o desperdício de produto e elimina a necessidade de limpar um recipiente antes de reciclar ou reutilizar.
Chamada de CleanTanX, a tecnologia é utilizada para tratar superfícies de tanques, funis e moegas, evitando que os materiais grudem nas laterais. O sistema pode reduzir o desperdício de material em até 99%.
“Isso pode realmente mudar o jogo. Ele economiza produtos desperdiçados, reduz as águas residuais geradas pelos tanques de limpeza e pode ajudar a tornar o processo de fabricação sem desperdício”, diz Varanasi, que atua como presidente da LiquiGlide.
Gostou? Então compartilhe: